RETURNS HANDLING
Returns
handling
Returns handling is the most expensive part of e-commerce logistics. It is the most expensive in several ways: the speed and accuracy of returns handling are aspects that strongly influence customer satisfaction; on the other hand, the sooner a returned product is put back into stock, the sooner it is available for sale again.
Even if you put a lot of energy into accurate product descriptions on your website and great images, you will still get returns. They are simply part of a logistics process that plays an important role in ensuring customer satisfaction (the so-called customer experience) and business efficiency.
The process involves a series of activities to receive, inspect, reproduce the product and packaging, put it back into the system, account for it and refund it. In the following text, I will outline some aspects of handling returns in logistics.
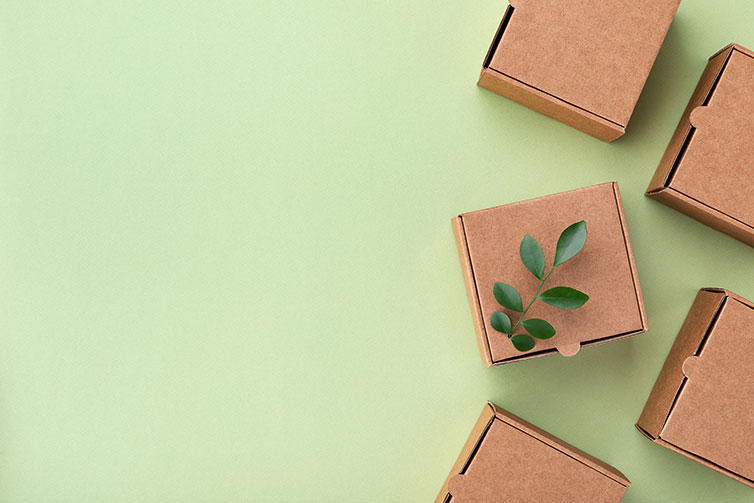
Key aspects
of returns handling
1. Accepting returns:
Returns handling is the most expensive stage of e-commerce logistics. It is the most expensive in several respects: the speed and accuracy of returns handling are aspects that strongly influence customer satisfaction; on the other hand, the sooner a returned product is returned to stock, the sooner it is available for sale again. Even if you put a lot of energy into accurate product descriptions on your website and great images, you will still get returns. They are simply part of a logistics process that plays an important role in ensuring customer satisfaction (the so-called customer experience) and business efficiency. The process involves a series of activities to receive, inspect, reproduce the product and packaging, put it back into the system, account for it and refund it. In the following text, I will outline some aspects related to the handling of returns in logistics.
2. Checking the goods
Once a return has been accepted, it is necessary to check the goods. Depending on the company’s policy, this may include checking the condition of the product, the original packaging, the completeness of the accessories, etc. The purpose of the inspection is to determine whether the goods meet the return requirements and whether the customer is entitled to a return. The returns process is different for cosmetics, clothing and electronics. We work with our customers to create returns processes that are ideal in their eyes.
3. Assess the reason for the return:
An important step in handling returns is to understand the reason for the return. This could be due to a product defect, a discrepancy with the order (although this doesn’t really happen at 4Values), the wrong size or some other issue. By analysing the reason for the return, you can identify potential areas for improvement to minimise future returns. It is also important to carefully record information about the cause of returns in order to monitor trends and take appropriate corrective action. This is also important for our customers as there will be a different process for returning advertised products, a different process for customer damaged products and a different process for unclaimed products.
4. Document processing:
An important step in handling returns is to understand the reason for the return. This may be due to a product defect, a discrepancy with the order (although this doesn’t really happen at 4Values), the wrong size or some other issue. By analysing the reason for the return, you can identify potential areas for improvement to minimise future returns. It is also important to carefully record information about the cause of returns in order to monitor trends and take appropriate corrective action. This is also important for our customers as there will be a different process for returning advertised products, a different process for products damaged by the customer and a different process for unclaimed products.
5. Receipt at the warehouse:
Once the return arrives at the warehouse, it must be accepted. Appropriate measures must be taken to inspect the product in order to integrate the returned goods into the existing range. Receipt at the warehouse includes checking quantity and quality and updating stock levels. It is also important that the goods are properly marked as returned for further processing and possible resale.
6. Returns processing:
Once the return has been accepted into the warehouse, it needs to be processed in the system. This involves updating stock records, possibly issuing an invoice adjustment and marking the goods as available for resale. Returns processing must be fast and accurate to minimise the time customers have to wait for a refund or product replacement.
7. Completing the returns process:
The final stage of returns processing is completion. This means that the goods have been processed correctly, the documentation is complete and the customer has received a refund or replacement product. It is also important to monitor customer satisfaction in order to assess the quality of the returns process and identify areas for further improvement.
Returns Management in Logistics the key to customer satisfaction and business efficiency
In summary, returns management in logistics is a complex process that requires precision, organisation and meticulousness. Ensuring a simple and convenient returns process, verifying the goods, processing the documents, analysing the reasons for returns, organising the return to the warehouse, receiving the return to the warehouse, processing the return and finalising the returns handling are all part of the process.
and closing the returns process are key elements of the process.
Attention to these aspects is critical to customer satisfaction and business efficiency.